Информационный дайджест №3
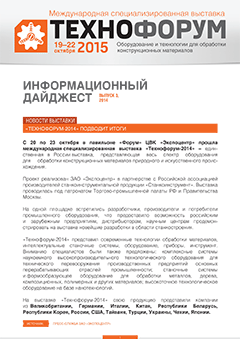
Новости выставки
«ТЕХНОФОРУМ-2014» подводит итоги
С 20 по 23 октября в павильоне «Форум» ЦВК «Экспоцентр» прошла международная специализированная выставка «Технофорум-2014» – единственная в России выставка, представляющая весь спектр оборудования для обработки конструкционных материалов природного и искусственного происхождения.
Проект реализован ЗАО «Экспоцентр» в партнерстве с Российской ассоциацией производителей станкоинструментальной продукции «Станкоинструмент». Выставка проводилась под патронатом Торгово-промышленной палаты РФ и Правительства Москвы.
На одной площадке встретились разработчики, производители и потребители промышленного оборудования, что предоставило возможность российским и зарубежным предприятиям, дистрибьюторам, научным центрам продемонстрировать на выставке новейшие разработки в области станкостроения.
«Технофорум-2014» представил современные технологии обработки материалов, интеллектуальные станочные системы, оборудование, приборы, инструмент. Вниманию специалистов были также предложены: комплексные системы наукоемкого высокопроизводительного технологического оборудования для технического перевооружения производственных предприятий основных перерабатывающих отраслей промышленности; станочные системы и формообразующее оборудование для обработки металлов, дерева, композиционных, полимерных и других материалов; высокоточное технологическое оборудование на базе нанотехнологий.
На выставке «Технофорум-2014» свою продукцию представили компании из Великобритании, Германии, Италии, Китая, Республики Беларусь, Республики Корея, России, США, Тайваня, Турции, Украины, Чехии, Японии.
Источник: Пресс-служба ЗАО «Экспоцентр»
«Станкопром» и Ассоциация «Станкоинструмент» провели совместную конференцию в рамках работы выставки «Технофорум-2014»
В ЦВК «Экспоцентр» в рамках работы выставки «Технофорум-2014» состоялась ставшая уже традиционной ежегодная конференция, проводимая ОАО «Станкопром» совместно с Ассоциацией «Станкоинструмент». В конференции приняли участие около 150 представителей более чем из 60 организаций.
Тема конференции: «Перспективные технологии и разработки высокотехнологичного наукоемкого оборудования предприятиями станкоинструментальной отрасли, отвечающие задачам реализации ФЦП «Развитие оборонно-промышленного комплекса РФ на 2011–2020 гг.».
От имени ОАО «Станкопром» выступил первый заместитель генерального директора Евгений Полканов с докладом на тему «Роль ОАО «Станкопром» в организации совместных разработок предприятий и НИИ оборонно-промышленного комплекса и отечественной станкоинструментальной промышленности в деле создания технологий опережающего развития (прорывных технологий)».
На конференции также обсуждались вопросы реализации постановления Правительства №1224, создания центра ультрапрецизионного станкостроения и уникальных технологий материалообработки, производства тяжелых и уникальных станков, создания современного металлорежущего оборудования для обработки деталей сложной формы, аддитивных технологий в машиностроении, импортозамещения систем управления в стратегически важных высокотехнологичных сферах металлообработки и многие другие.
Источник: www.stankoprom.ru
События отрасли
По заказу Минпромторга разработают дорожную карту развития военных роботов
Министерство промышленности и торговли объявило тендер по исследованию путей развития робототехники в интересах обороноспособности страны. Заявка ведомства размещена на сайте госзакупок.
Цель работы – создание дорожной карты развития робототехники военного и специального назначения на период до 2030 года. Победитель тендера изучит отечественный и зарубежный опыт использования передовых технологий при создании робототехники для экстремальных условий.
Победитель тендера должен будет спрогнозировать развитие соответствующих промышленных технологий.
Кроме того, необходимо разработать рекомендации по внедрению и развитию промышленных технологий, используемых в робототехнике, а также подготовить предложения по тематике исследований для проектов госпрограмм по развитию оборонно-промышленного комплекса РФ в части военной и специальной робототехники.
Работа должна быть выполнена до 20 декабря следующего года. Итоги конкурса будут подведены 29 октября. Начальная (максимальная) цена госконтракта – 20 млн рублей.
Источник: minpromtorg.gov.ru
«Станкопром» представил разработки в рамках программы импортозамещения для техперевооружения ОПК
На площадке Савеловского машиностроительного завода 17 предприятий станкоинструментального холдинга «Станкопром» (входит в Госкорпорацию «Ростех») продемонстрировали достижения отрасли представителям оборонно-промышленного комплекса.
Мероприятие прошло в соответствии с недавним решением Правительства, согласно которому «Станкопром» должен стать Инжиниринговым центром компетенций и локомотивом процесса внедрения в производство отечественных станков.
«Уже с текущего года для оборонных предприятий, которые получают бюджетные деньги на закупку станков, мы установим минимально допустимый уровень оснащенности российским технологическим оборудованием на уровне 10% от их потребностей. В последующие годы этот показатель будем плавно увеличивать, чтобы к 2020 году он достиг 60%», – отметил в своем обращении к делегатам министр промышленности и торговли Денис Мантуров.
За последние 4 года в рамках реализации программы «Развитие отечественного станкостроения и инструментальной промышленности на 2011–2016 годы» разработаны около 100 образцов новых станков и высокотехнологичного твердосплавного сборного инструмента, которые полностью готовы к внедрению в производство.
В своем выступлении генеральный директор «Станкопрома» Сергей Макаров подчеркнул: «Ключевая задача «Станкопрома» – качественно изменить подход к технологическому перевооружению российских предприятий. Продемонстрированные сегодня достижения позволяют надеяться, что мы сможем не только обеспечить выполнение правительственной программы до 2016 года, но и решить вопрос импортоопережения в ОПК за счет использования передовых российских образцов. А они, в свою очередь, по ряду показателей превосходят зарубежные аналоги».
Среди представленных образцов особое внимание представители оборонной промышленности уделили образцам перспективного станкоинструментального оборудования, замещающего импортные аналоги массового потребления, – токарно-фрезерным обрабатывающим центрам с ЧПУ, универсальным токарно-винторезным, сверлильно-расточным и другим станкам, а также современному твердосплавному режущему инструменту для высокоскоростной и силовой резки различных сплавов, сталей и композиционных материалов. На внедрение представленного оборудования в промышленных масштабах потребуется от двух до трех лет.
Другим интересным экспонатом стал промышленный образец высокоточного шпинделя на аэростатических опорах, являющегося ключевым узлом для импортозамещающих многокоординатных ультрапрецизионных шлифовальных, фрезерных и токарных обрабатывающих центров модульной конструкции, предназначенных для обработки деталей с погрешностями размеров менее 100 нм, шероховатостью поверхности менее 5 нм и точностью формы порядка 50 нм.
Такие точные характеристики необходимы для обеспечения потребностей российских высокотехнологичных производств, прежде всего, предприятий аэрокосмической, атомной, медицинской промышленности, научно-исследовательских центров и институтов РАН, оптических и приборостроительных предприятий ОПК, в технологическом оборудовании и технологиях для получения ультрапрецизионных деталей, в том числе с микроструктурами из различных материалов, включая труднообрабатываемые.
Всего в ходе мероприятия свои достижения показали практически все крупные предприятия России, включая Савеловский, Волжский, Стерлитамакский машиностроительные заводы, Рязанский станкостроительный завод, Ивановский завод тяжелого станкостроения, Кировградский завод твердых сплавов, «САСТА», ВСЗ «Техника», «Группа Стан», «ВНИИИНСТРУМЕНТ», «МСЗ-Салют», «СП «Донпрессмаш», «Липецкое станкостроительное предприятие», МГТУ «СТАНКИН» и другие.
Источник: www.stankoprom.ru
Созданный НИЦ объединит ресурсы пяти ведущих исследовательских институтов страны в области авиастроения
Законопроект «О Национальном исследовательском центре «Институт имени Н.Е. Жуковского» (НИЦ)», принятый Госдумой 17 октября, нацелен на концентрацию усилий и ресурсов (прежде всего интеллектуальных) пяти ведущих исследовательских институтов страны в области авиастроения.
Об этом заявил спикер палаты Сергей Нарышкин, на его слова ссылается информационное агентство РИА «Новости».
Центр будет осуществлять научно-исследовательскую деятельность, разработки и научное сопровождение внедрения новых технологий, участие в подготовке научных кадров, прогнозирование научного и технологического развития России в области авиастроения, а также подготовку предложений по координации научно-исследовательской, научно-технической и производственной деятельности организаций в интересах крупных инновационных проектов.
Органами управления центра станут наблюдательный совет, генеральный директор и правление. В состав наблюдательного совета войдут 15 человек, избираемые сроком на пять лет: представитель президента России, представители Федерального собрания, представители Правительства России, представитель РАН, представители организаций промышленного и оборонно-промышленного комплексов и генеральный директор центра.
В центре будет создан экспертный совет для научно-методического, информационно-аналитического и экспертного обеспечения деятельности.
Центр создается в форме федерального государственного бюджетного учреждения.
В законе также прописано, что будет разработан план деятельности центра, утверждаемый Минпромторгом и правительством, по развитию науки и технологий в авиастроении, в котором будут определяться целевые показатели, основные направления и задачи развития.
Источник: minpromtorg.gov.ru
«Станкопром» и администрация Тверской области договорились о сотрудничестве
Сергей Макаров, генеральный директор ОАО «Станкопром» (входит в состав Госкорпорации «Ростех»), и Андрей Шевелев, губернатор Тверской области, подписали соглашение о развитии станкоинструментальных производств и организации долгосрочного сотрудничества в области технического перевооружения машиностроительных предприятий Тверской области.
В рамках соглашения планируется разработка и реализация проектов по созданию на территории Тверской области новых станкостроительных и инструментальных предприятий, механизмов участия ОАО «Станкопром» в проектах по техническому перевооружению машиностроительных предприятий региона, совместное привлечение иностранных партнеров для проработки вопросов трансфера технологий и локализации производства импортной станкоинструментальной продукции на территории Тверской области.
Со своей стороны, Правительство Тверской области проработает вопрос о компенсации части процентной ставки по кредитам и возможности соинвестирования реализуемых «Станкопромом» совместно с предприятиями области инвестиционных проектов по созданию станкоинструментальных производств.
«В рамках проводимой Правительством России политики импортоопережения перед «Станкопромом» поставлена задача по выработке мер по обеспечению технологической независимости машиностроительных предприятий за счет конкурентной импортозамещающей продукции отечественного производства», – заявил гендиректор «Станкопрома» Сергей Макаров. «В этом направлении мы намерены развивать отношения с Тверской областью и другими промышленными регионами».
«Сегодня машиностроение является основным сегментом экономики региона, который дает более четверти всей промышленной продукции. Савеловский машиностроительный завод, который входит в состав холдинга «Станкопром», – одно из крупнейших российских предприятий в своей сфере. Здесь накоплен бесценный опыт проектирования и производства уникального оборудования, создана мощная производственная и научно-исследовательская база, что позволяет выполнять целый спектр стратегических задач для отечественной экономики. Я уверен, что мы вместе делаем первый шаг в новую эпоху развития для всех станкопроизводящих предприятий региона», – подчеркнул в своем выступлении губернатор Тверской области Андрей Шевелев.
Соглашение станет основой долгосрочного, тесного и плодотворного сотрудничества между Правительством Тверской области и системным интегратором станкостроительной отрасли ОАО «Станкопром».
Ранее соглашения о сотрудничестве «Станкопром» подписал с администрациями Владимирской, Тульской и Липецкой областей.
ОАО «Станкопром» – холдинговая компания Госкорпорации «Ростех», специализирующаяся на станкостроении и инструментальном производстве. ОАО «Станкопром» – системный интегратор станкостроительной отрасли, объединяет сохранившиеся государственные производственные, научные, инструментальные и коммерческие организации отрасли. По инициативе Министерства промышленности и торговли Российской Федерации и Госкорпорации «Ростехнологии» консолидированы ведущие российские станкостроительные предприятия, расположенные в восьми регионах России.
Государственная корпорация «Ростех» – российская корпорация, созданная в 2007 году для содействия разработке, производству и экспорту высокотехнологичной промышленной продукции гражданского и военного назначения. В ее состав входит около 700 организаций, из которых в настоящее время сформировано 9 холдинговых компаний в оборонно-промышленном комплексе и 5 – в гражданских отраслях промышленности. Организации «Ростеха» расположены на территории 60 субъектов РФ и поставляют продукцию на рынки более 70 стран. Выручка «Ростеха» в 2013 году составила 1,04 трлн рублей, чистая прибыль – 40 млрд рублей. Налоговые отчисления в бюджеты всех уровней превысили 138 млрд рублей.
Источник: www.rostec.ru
На «Климове» начал работу новый конструкторско-производственный комплекс
20 октября 2014 года на площадке разработчика двигателей «Климов» состоялось торжественное открытие первой очереди современного конструкторско-производственного комплекса, приуроченное к 100-летию компании.
Торжественная церемония прошла при участии заместителя министра промышленности и торговли Российской Федерации Юрия Слюсаря, исполняющего обязанности губернатора Санкт-Петербурга Александра Говорунова, генерального директора ОПК «Оборонпром» Дмитрия Леликова, генерального директора Объединенной двигателестроительной корпорации Владислава Масалова, исполнительного директора ОАО «Климов» Александра Ватагина.
Заместитель министра промышленности и торговли России Юрий Слюсарь поблагодарил работников завода за проделанную работу. «Все мы знаем о задачах масштабного наращивания производства авиационных двигателей, а также выполнения гособоронзаказа. Уверен, что с появлением подобных производств они будут успешно решены», – сказал замминистра.
Генеральный директор ОПК «Оборонпром» Дмитрий Леликов подчеркнул, что «перед ОДК и «Климовым», в частности, стоят новые задачи как по освоению серийного выпуска вертолетных двигателей ТВ3-117 и ВК-2500, так и по разработке перспективного двигателя для скоростного вертолета. Сегодня у предприятия есть все возможности для этого: и собственное конструкторское бюро, и самая современная в ОДК производственная площадка».
«Юбилей «Климова» выдался на очень непростое время. Реализация программы импортозамещения, которая сейчас идет на предприятии, – необходимое условие укрепления обороноспособности страны. Но в то же время это и трамплин для полномасштабных преобразований. Именно здесь, на этой площадке, мы закладываем новые принципы индустриальной модели нашей корпорации, успешная реализация которых позволит создавать конкурентоспособные двигатели как по техническим, так и по экологическим параметрам», – отметил в своей поздравительной речи генеральный директор ОДК Владислав Масалов.
Исполнительный директор «Климова» Александр Ватагин, говоря об открытии первой очереди современного конструкторско-производственного комплекса, отметил, что реализация проекта «Петербургские моторы» – старт для дальнейшего развития предприятия и корпорации. «Благодарю всех, кто участвовал в данном проекте. Это труд многих и многих людей. Поздравляю коллектив со 100-летием ОАО «Климов», – отметил Александр Ватагин.
В рамках торжественной церемонии также состоялось открытие памятника Владимиру Яковлевичу Климову – советскому конструктору авиационных двигателей, чье имя теперь носит завод.
Сотрудникам «Климова» были вручены награды Министерства промышленности и торговли России и «Ростеха».
Справка
ОАО «Климов» – дочерняя компания Объединенной двигателестроительной корпорации, входящей в Госкорпорацию «Ростех». Это ведущий российский разработчик газотурбинных двигателей для большинства вертолетов марки «Миль» и «Камов», а также реактивных двигателей для истребительной авиации. Сегодня «Климов» расширяет номенклатуру разрабатываемых и производимых изделий, реализуя программу импортозамещения и участвуя в программе организации серийного производства самолета Ил-114.
С января 2010 года ОДК на базе «Климова» реализует проект строительства конструкторско-производственного комплекса инновационного типа, рассчитанного на выпуск серийных газотурбинных двигателей ежегодным объемом до 500 шт. Совокупный объем в проект КПК превышает 6 млрд рублей.
ОАО «Объединенная двигателестроительная корпорация» – дочерняя компания ОПК «Оборонпром». В структуру ОДК интегрированы более 85% ведущих предприятий, специализирующихся на разработке, серийном производстве и сервисном обслуживании газотурбинной техники, а также ключевые предприятия – комплектаторы отрасли. Одним из приоритетных направлений деятельности ОДК является реализация комплексных программ развития предприятий отрасли с внедрением новых технологий, соответствующих международным стандартам.
Государственная корпорация «Ростех» – российская корпорация, созданная в 2007 году для содействия разработке, производству и экспорту высокотехнологичной промышленной продукции гражданского и военного назначения. В ее состав входит около 700 организаций, из которых в настоящее время сформировано девять холдинговых компаний в оборонно-промышленном комплексе и пять – в гражданских отраслях промышленности. Организации «Ростеха» расположены на территории 60 субъектов РФ и поставляют продукцию на рынки более 70 стран. Выручка «Ростеха» в 2013 году составила 1,04 трлн рублей, чистая прибыль – 40 млрд рублей. Налоговые отчисления в бюджеты всех уровней превысили 138 млрд рублей.
Источник: minpromtorg.gov.ru
Как печатают детали
Прототипирование – дело это относительно новое, и далеко не все знают, что оно из себя представляет и что с его помощью можно печатать не только детали для механизмов, но даже живые биологические органы.
Неотъемлемой частью создания сложных архитектурных и технологических объектов является моделирование. Сначала макет разрабатывается в электронном виде – виртуально, после чего его обязательно следует воплотить в реальной, твердой копии. Ранее на это уходило несколько недель или даже месяцев, требовался труд многих специалистов.
Теперь на смену традиционным технологиям пришло быстрое прототипирование. С его помощью точный макет различных деталей и изделий или опытный образец для демонстрации полезных свойств предмета можно получить за несколько дней, часов или даже минут – в зависимости от их сложности.
Термин «быстрое прототипирование» (Rapid Prototyping, RP) часто заменяют словосочетанием «трехмерная печать» (3D-printing, 3DP). Оно более понятно и привычно, но менее точно отражает суть процесса. В принципе, работу обычного офисного принтера тоже можно назвать «двухмерной печатью», или 2D-printing, но в жизни так практически никто не говорит.
Трехмерный, или 3D-принтер – это устройство вывода трехмерных данных, результатом его работы является некоторый трехмерный физический объект. Существует несколько технологий объемной (трехмерной, 3D) печати, но в основе любой из них лежит принцип послойного создания, построения или «выращивания» твердой физической конструкции по электронным данным математической (компьютерной) модели.
Основной сферой применения технологии прототипирования является промышленность. Быстрое изготовление прототипов изделия позволяет увидеть, как оно будет выглядеть в материале. На модели можно проводить различные тесты еще до того, как будет готов окончательный вариант изделия. Причем некоторые тесты следует проводить только на прототипе – на готовом изделии это невозможно или не рекомендуется. Например, прозрачная пластиковая модель трансмиссии 911 GTI была использована Porsche в процессе ее разработки для изучения тока масла.
Быстрое прототипирование – идеальное решение для малосерийного производства (от пары штук до нескольких тысяч). Оно просто незаменимо при изготовлении опытных, единичных, эксклюзивных и уникальных образцов, при необходимости частых изменений в дизайне или конструкции деталей, при старте запуска серийных изделий, при изготовлении форм для литья.
Сегодня прототипирование можно встретить практически повсюду. Данная технология используется в машиностроении и полиграфии, в электротехнической и электронной промышленности, в медицине, ювелирном деле и архитектуре. Уже сейчас прототипирование доступно многим на бытовом уровне в виде недорогой услуги, которой может воспользоваться каждый. Достаточно нарисовать модель, определить материал и отправить заказ по Интернету. Это называется «дистанционное производство по требованию» (Distance Manufacturing on Demand).
А в перспективе такая технология станет массовой: у каждого на столе будет свой персональный механический заводик, заменяющий в мелочах обычное производство. Точно так же, как принтеры заменили типографии и машинописные бюро.
В этой области постоянно происходит что-то новое и неожиданное. Так, группа ученых из Калифорнийского университета в Беркли разрабатывает технологию одновременной трехмерной печати и формы, и содержания объекта: к примеру, корпуса мобильного телефона и его электронной начинки.
А в Университете Миссури работают над технологией выращивания биологических органов – при помощи того же струйного 3D-принтера. В качестве чернил используются сгустки клеток заданного типа, а «бумагой» выступает специальный биогель, который фиксирует положение клеточных сгустков в пространстве.
В Москве в декабре 2013 года при участии двух вузов, НИУ ВШЭ и МАТИ, открылся очередной Центр молодежного инновационного творчества (FabLab), занимающийся именно прототипированием. Здесь можно не только освоить основы этой специальности, но и опробовать свои идеи, сделать задуманную вещь самостоятельно или с помощью специалиста.
«Мы должны как минимум научиться пользоваться такими технологиями. А как максимум – стать законодателями мод – производителями подобных технологий, которые в настоящий момент в мире активно развиваются», – сказал руководитель ГБУ «Центр инновационного развития» (ЦИР) Константин Фокин.
По материалам сайта www.rostec.ru
Исследования
Новые шаги на пути создания вечного двигателя
Наука о трении: машины будущего станут напоминать фантастических животных. Трение может быть полезным. Это свойство исследуется новым прорывным направлением науки о трении – трибологией на основе синергетики (самоорганизации).
О вреде трения в машиностроении известно всем. Это и износ деталей (причина 95% случаев поломок машин). И расход энергии (более половины потребляемого топлива идет на преодоление сопротивления при трении). И лишние траты (расходы на ремонт авиатехники, к примеру, превышают ее стоимость в 5 раз, а станков – и вовсе в 8 раз). И нагрузка на окружающую среду (для замены изношенного оборудования требуется выплавлять все больше чугуна и стали).
А вот о том, что трение может быть полезным, знают единицы. Если вы не из их числа, не огорчайтесь – ученые и сами сделали это открытие совсем недавно.
Новое направление трибологии все исследователи в один голос называют прорывным, стратегическим. Оно изучает созидающее действие трения на основе синергетики (или самоорганизации).
Научной базой для этого направления стали два открытия мирового уровня: «эффект безызносности при трении» (1964 год) и «водородное изнашивание металлов» (1992 год). Автором открытий и основателем этой научной школы является выдающийся российский ученый – профессор, академик Российской инженерной академии Дмитрий Николаевич Гаркунов.
Суть трибологии на основе самоорганизации – в особом взаимодействии регулярной микрогеометрии детали и металлоплакирующей присадки. Регулярная микрогеометрия – это специальные неровности, искусственно создаваемые на поверхностях трущихся частей, система микровыступов и микровпадин правильной формы. Металлоплакирующая присадка – специальная добавка к смазке, содержащая наночастицы квазижидкостной меди.
Наночастицы меди заполняют шероховатости стальных или чугунных деталей, заменяя трение чугун – сталь или сталь – сталь, трением меди по меди, что снижает коэффициент трения в узлах с 0,1–0,05 до 0,03–0,003. Кроме того, в результате взаимодействия данной смазки и таких специальных шероховатостей на поверхностях трущихся деталей самопроизвольно возникает особая, защитная, непрерывно возобновляющаяся, так называемая сервовитная медная пленка, обладающая феноменальными физическими свойствами.
Пленка появляется за счет тепловой и электрической энергии, выделяющейся при трении, и химического взаимодействия элементов. В итоге процесс трения из разрушительного становится созидательным, подобным движению суставов в скелетах живых организмов, где тоже имеются трущиеся поверхности и аналог металлоплакирующей смазки – хрящевая ткань и сиовиальная жидкость.
Данное направление науки о трении привлекает все большее внимание ученых во всем мире. В России, в Московском государственном техническом университете имени Н.Э. Баумана в настоящее время формируется научная школа по трибологии на основе самоорганизации.
Для проведения научной и исследовательской работы здесь оборудовали специальную лабораторию триботехники. В ней разрабатываются новые виды металлоплакирующих смазок, создаются новые способы их испытания. Планируется создание малого предприятия по лицензированию смазочных материалов.
Недавно на межрегиональном научно-практическом семинаре «Итоги реализации эффекта безызносности в процессах металлообработки и эксплуатации», который состоялся в Орехове-Зуеве на научно-производственном предприятии «Респиратор», входящем в холдинг «Авиационное оборудование», ученые обсуждали данные последних испытаний моторных масел с металлоплакирующей присадкой в Норвегии и Германии. Эффект от их применения очевиден: расход топлива за счет уменьшения потерь на трение сокращается до 23%.
Новые триботехнологии находят все более широкое применение в транспорте, авиации и флоте, химическом и металлообрабатывающем секторе, тяжелом машиностроении и сельскохозяйственной технике. Их использование уже сегодня позволяет:
- повысить ресурс машин и оборудования почти в два раза;
- сократить расход смазочных материалов в 2–3 раза;
- снизить количество аварий за счет повышения надежности работы узлов трения;
- снизить потребление запасных частей в два и более раз;
- снизить загазованность атмосферы при работе транспорта в 2–3 раза.
А в будущем на основе новых нанотрибоматериалов и нанотриботехнологий ученые предполагают создавать такие закрытые долговечные универсальные узлы трения, которые по своему физико-химическому механизму практически ничем не будут отличаться от суставов живых организмов с их естественной самоорганизацией. Другими словами, в технике все больше станут использоваться природные механизмы, а машины все больше станут напоминать животных.
Источник: www.rostec.ru